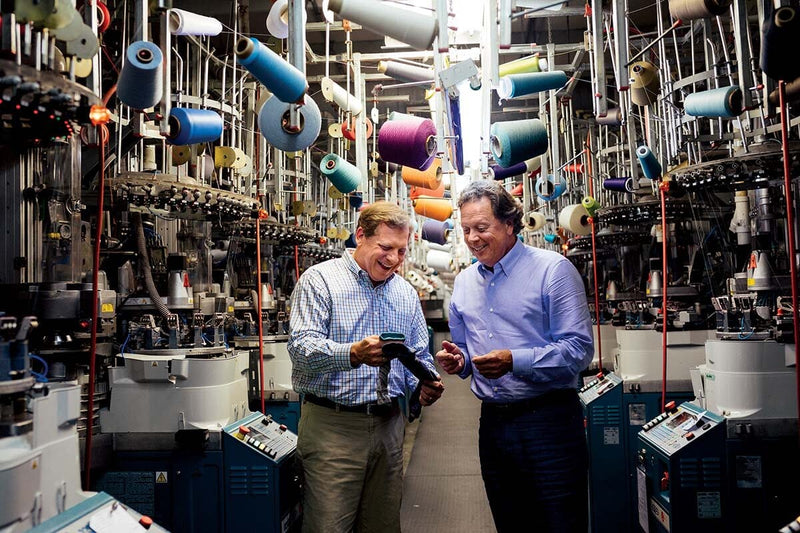
Quality product, American-made.
Written by: Thomas Lee, Partner and Yarn Designer
Quality product, American-made—these are founding principles of the Sockwell brand, which give us great pride in the footprint of how our socks are made: right here in the USA.
We've partnered with American manufacturing partners to craft every sock domestically since the start of Sockwell. We source our wool from American wool growers, and it is then treated and spun into yarn in South Carolina. These yarns are then transported and dyed in North Carolina, to finally be knitted at the plants located in North Carolina and Tennessee—one of which resides around the corner from the home of our headquarters, in Chattanooga, TN.
Our Chattanooga mill, Heritage Hosiery, is a family-owned mill that has been in business since August 1996. Heritage is filled with state-of-the-art, Italian manufactured knitting machines capable of producing the cutting-edge products that we require for Sockwell socks.
And with great machinery comes the great people who operate them. That’s why we want to introduce and acknowledge the hands of the hardworking men and women at this local Chattanooga business. We’re thrilled to take you through the step-by-step assembly of how are socks are made in a factory, from the program to the details, and showcase the faces that lace each thread with care, passion and dedication.
Step One: Building the Program for Each Sock
In a nutshell, the “program” tells the knitting machine how to make each sock. And for Sockwell socks, this is where Heidi Hinton comes into play.
As the product development technician at Heritage Hosiery, Heidi takes the sock specifications developed by Sockwell designer, Mercedes Marchand, and the Sockwell product team, and translates the design into the knitting machine program. Our specifications include everything from sock height and compression level, to the yarn types and colors.
Heidi has been in the sock manufacturing business for over 20 years, with the last 18 being at Heritage. Heidi began as a sock inspector, progressed into knitting and ultimately moved to machine technician, otherwise known as a “fixer.” For the last six years, Heidi has directed her talents toward product development, where she has been instrumental in working with Sockwell to create many of the unique, wool-based products our customers have grown to love.
When Heidi is not pushing the envelope of new product design and development, she’s strumming tunes on her acoustic and electric guitars or spending time with her family.
Step Two: Procuring Materials
Once the sock has been developed, approved, and ordered for production, the order makes its way to the desk of April Bryson. April handles all purchasing for Heritage, meaning she’s the glue that keeps production together.
We launch new styles two times per year and a large variety of colors each season across four categories of socks, all in different packaging. April has the challenging task of managing not only the 300 different yarns it takes to make each unique combination of socks, but also the myriad packaging and labeling materials used to encase each product.
Through all of these moving pieces, we’re grateful one thing has remained constant: April’s dedication to keep our materials stocked and our process smooth.
April has been in her current purchasing role at Heritage for two years and comes to Heritage after a 10-year stint working in quality control and inside sales in different industries. She was born in Fort Payne, Alabama, and has lived most of her life in North Georgia. When April is not ordering yarn and packaging, she enjoys practicing Jiu-Jitsu and reading books, in particular anything written by Steven King. April is married and is the proud parent of two teenage children.
Step Three: Knitting Socks
After all of the required raw materials are obtained, it is time to move to the knitting process. The knitting machine is outfitted with the unique yarn that makes up an individual sock, which typically requires between 10 to 20 different yarns. The program is then loaded in by the machine technician or “fixer” who completes the machine setup and launches the machine into action.
At Heritage, this duty falls to LeBron Higdon, a senior knitting machine technician. LeBron completes the machine setup and checks the product quality to ensure it is se with the correct yarns and sized to fit properly. After this is verified, the machine moves into production, and anywhere between 6 to 10 pairs of socks are produced per hour.
LeBron hails from a small town that shares his family name—Higdon, Alabama. Prior to coming to Heritage, LeBron was a diesel mechanic at an industrial machinery dealership; now he’s beginning his tenure at Heritage as a fixer trainee, with 9 years of experience under his belt. When he’s not spending time with his family, LeBron loves to spend his free time embracing fresh air while catching fish on Nickajack Lake.
Step Four: Double-Checking the Details
The knit socks then proceed to the finishing department where they are washed, dried and boarded, giving each sock its neat, finished appearance. Finally, they are packaged into our signature Sockwell packaging and sent out for delivery.
All of the production process is overseen by the quality control department. At every step of the process, product is checked by the QC department staff to ensure it meets our exacting quality standards. At Heritage, the QC team is headed by Karen Walker, who has been with the company for 12 years now. She began her sock career “creeling,” which is the process of putting all of the required yarns on to the knitting machine, and from there, she moved on to supervision, and ultimately, into quality control.
As you would expect from a top-notch QC administrator, Karen takes great pride of ownership in her work. No detail is too small to warrant her attention when it comes to ensuring the product is perfect. When Karen is not making socks, she loves to relax, watch movies and crochet. She is the proud mother of 4 children and 10 grandchildren who range in age from two to 20!
It’s no doubt, the production process is a laborious journey. Each step is handled with great care and attention to detail. As they say, it takes a village, and we’re so appreciative of everyone who plays a role in this small-scale, yet world class, sock-making village of ours.